New 3D-printed front air inlet made with Windform composite materials
CRP Technology recently developed a new front air inlet for a Moto3 racing customer, which was manufactured in Windform materials by using an SLS additive manufacturing technique.
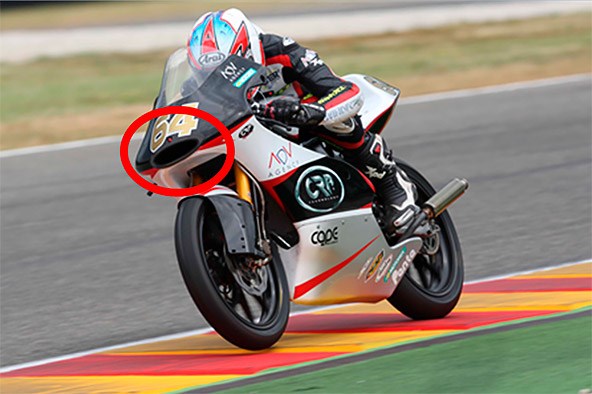
Outlined in red, the front air inlet similar to the one produced in Windform. (Photo: CRP Technology)
Earlier this year, we reported that additive manufacturing provider CRP Technology (part of CRP Group Modena, Italy) had launched Windform RL, the first thermoplastic elastomer material within the Windform family of materials for professional 3D printing.
Now CRP’s R&D department said that it recently developed a new front air inlet for a Moto3 racing customer, which was manufactured in Windform materials by using an SLS additive manufacturing technique.
According to CRP Technology, testing had shown that increasing air flow to the air-box improved the performance of the engine at every RPM range. This led the team as well as the engineers to conclude that they need to design a new track ready inlet. This design would make the air inlet longer, and bring the opening up to the front side of the fairing, in order to have a direct air flow with less turbulence.
CRP wanted to avoid modifying the existing frame and the existing triple clamps. The design would have to fit to the existing platform in order to test the on-track advantages and disadvantages of using this solution, and to make a direct comparison with the current standard inlet.
The project
Once a first draft of the air inlet was developed, a prototype in Windform GF 2.0, which is a composite material with a polyamide base filled with glass and aluminum, was created. The decision to use Windform GF 2.0 was made to reduce costs, while being able to perform multiple tests with multiple prototypes.
The first prototype allowed engineers to see if the design fitment was correct and suitable for assembly. It was revealed by the first design that some sections needed to be changed due to the lack of space available under the lower triple clamp. This problem is further complicated when the bike is cornering and under braking conditions.
To optimize the volume of the inlet duct under the lower triple clamp, the engineers adopted a creative approach and decided to use a portion of the duct in Windform RL, the new rubber-like composite material produced by CRP Technology. This would be bonded to the main structure that was made out of Windform XT 2.0 for evaluation in racing conditions. To facilitate this, they also carried out a bonding test to study the characteristics of the final assembly.
The concept was to make the bottom part of the duct with Windform RL in the fork and triple clamp area, and then assemble this into the top part produced in Windform XT 2.0. This approach would allow good clear airflow on the straightaway sections of the course, and thus an excellent flow to the airbox. Under breaking, the front fender could move up and collapse the inlet duct without any damages, due to the flexible material.
The team and engineers eventually decided to change the inlet by reducing the portion that would make contact with the fender to reduce drag perceived by the rider. The part made in Windform RL was enlarged according to the second test, and engineers and the rest of the team could get the correct fit for performance.
In the final test version, Windform XT 2.0 was utilized in order to reduce the weight of the front and central part of the inlet, while the Windform RL material was used for the flexible part of the inlet. The two parts were bonded together after being produced.
Front air inlet (final version) after testing.
Related Content
“Structured air” TPS safeguards composite structures
Powered by an 85% air/15% pure polyimide aerogel, Blueshift’s novel material system protects structures during transient thermal events from -200°C to beyond 2400°C for rockets, battery boxes and more.
Read MoreJeep all-composite roof receivers achieve steel performance at low mass
Ultrashort carbon fiber/PPA replaces steel on rooftop brackets to hold Jeep soft tops, hardtops.
Read MoreCarbon fiber, bionic design achieve peak performance in race-ready production vehicle
Porsche worked with Action Composites to design and manufacture an innovative carbon fiber safety cage option to lightweight one of its series race vehicles, built in a one-shot compression molding process.
Read MoreThermoplastic composites: Cracking the horizontal body panel nut
Versatile sandwich panel technology solves decades-long exterior automotive challenge.
Read MoreRead Next
Plant tour: Daher Shap’in TechCenter and composites production plant, Saint-Aignan-de-Grandlieu, France
Co-located R&D and production advance OOA thermosets, thermoplastics, welding, recycling and digital technologies for faster processing and certification of lighter, more sustainable composites.
Read MoreAll-recycled, needle-punched nonwoven CFRP slashes carbon footprint of Formula 2 seat
Dallara and Tenowo collaborate to produce a race-ready Formula 2 seat using recycled carbon fiber, reducing CO2 emissions by 97.5% compared to virgin materials.
Read MoreDeveloping bonded composite repair for ships, offshore units
Bureau Veritas and industry partners issue guidelines and pave the way for certification via StrengthBond Offshore project.
Read More