Airtech 3D-printed resins deliver composite tooling for competitive motorsport vehicles
BBi Autosport joins with Airtech Advanced Materials Group to develop high-performance carbon fiber body panels for its Porsche race cars using Dahltram resins and Print-Tech services.
Share
Read Next
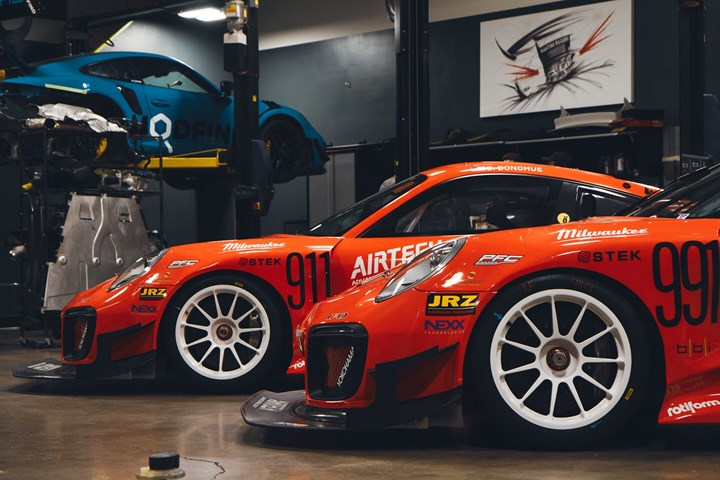
Photo Credit: BBi Motorsport
BBi Autosport (Huntington Beach, Calif., U.S.) is returning to Pikes Peak, Colorado, for the 99th running of the Pikes Peak International Hillclimb on June 27, 2021. Known as “The Race to the Clouds,” the automobile hill climb is regarded as one of the most famous and arduous racing events globally. For this year’s 2021 effort, BBi says it is bringing three Porsche race cars, all of which make extensive use of carbon fiber composites and 3D-printing technologies.
The high-performance vehicles’ carbon fiber composite body panels were produced using 3D-printed mold tooling manufactured by BBi technical partner, Airtech Advanced Materials Group (Huntington Beach, Calif., U.S.), as well as Airtech’s Dahltram range of resins and Print-Tech in-house tooling 3D print service. Motorsports programs require rapid development cycles, BBi Autosport says, and with Print-Tech, molds are able to be produced much more quickly. This advantage further enables aerodynamic development and part manufacturing to be completed in weeks, rather than months.
Airtech’s Dahltram range of resins have been made distinctly suitable for multiple print platforms, providing production flexibility with end use material approvals. Continuous thermal cycle testing, pressure leak testing, laser surface scanning and contact material testing have generated data supporting more than 250 autoclave cycles, Airtech says, without degradation of the Dahltram manufactured tooling.
Airtech’s retains Dahltram additive manufacturing resins and Print-Tech large-scale 3D-printed tool manufacturing capabilities in the U.S. and Europe.
Related Content
-
Sulapac introduces Sulapac Flow 1.7 to replace PLA, ABS and PP in FDM, FGF
Available as filament and granules for extrusion, new wood composite matches properties yet is compostable, eliminates microplastics and reduces carbon footprint.
-
The next evolution in AFP
Automated fiber placement develops into more compact, flexible, modular and digitized systems with multi-material and process capabilities.
-
Large-format 3D printing enables toolless, rapid production for AUVs
Dive Technologies started by 3D printing prototypes of its composite autonomous underwater vehicles, but AM became the solution for customizable, toolless production.