BM Composites announces the launch of the Linx 30 Superyacht Tender
The first custom tender brand designed and made in Mallorca, Spain, highlights the customizable Linx 30, a carbon fiber infused superyacht with 30-40% improved fuel efficiency.
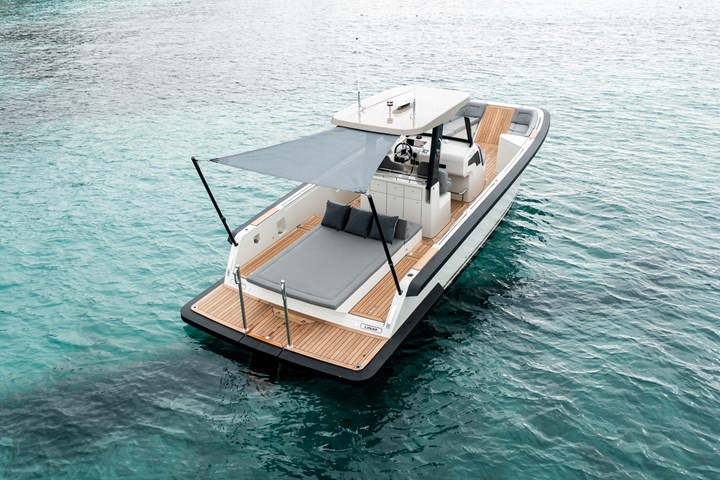
The Linx 30 with a customizable E-deck. Photo Credit, all images: BM Composites
The Linx 30 Superyacht Tender, said to be the first custom tender brand built by Palma composites specialists BM Composites (Spain), was recently launched at the Palma International Boat Show at the end of April. High-speed performance and stability are complemented by a carbon fiber structure and a fully customizable deck configuration, BM Composites says, in addition to a state-of-the-art, foil-assisted catamaran hull with 30-40% improved fuel efficiency. The Linx created interest from press to brokers and private boat buyers, and new orders are already in development.
The Linx is also reported to be the first superyacht tender to be designed and built in Mallorca. Highly regarded local naval architect Tià Simó of Bravo Yacht Design (Barcelona, Spain) was involved in the project from design conception to sea trial and worked to a tight brief, balancing the client’s demand for stability, high performance and a strictly controlled weight limit. The Linx was commissioned by an expedition mega yacht who also specified key features including a beach landing system, a folding hardtop for garage stowage inside the mothership and a WASSP sonar integration. The explorer vessel often navigates in uncharted waters and the Linx tender will serve as a scout by transmitting topographic data of the seabed back to the mothership via the integrated multi-beam sonar system.
The prototype Linx 30, offering a layout for 12 passengers, was built with composites, using Gurit’s (Wattwil, Switzerland) Prime 37 infusion resin system and Corecell marine foam. The hull is said to be a high-tech tour de force, displacing 3.5t, including 430lt of diesel and covering 130 nautical miles at a cruising speed of 25 knots. BM Composites' manufacturing facility has been approved as a CE-certified shipyard and the Linx 30 as a CE-certified C-Class boat.
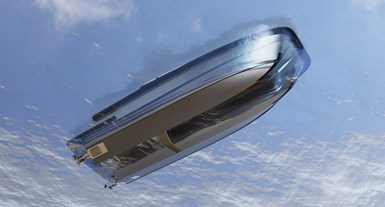
Linx 30 underwater foils.
A large proportion of design time went into fluid dynamic testing of the hull shape and foil configuration, combining speed and longitudinal stability with a wave-dampening effect generated by the foils. “By reducing drag, the foil improves seakeeping and gives up to 40% more speed for the same power and fuel consumption,” Mark Branagh, managing director of BM Composites, explains. The Linx has a large, fixed foil between the two hulls and two trim tabs right aft providing the lift which maximizes the fuel saving benefits.
Moreover, the tender is fully customizable — deck layout, helm console, engines and propulsion system can all be designed to customer specifications. Linx 30 can be configured as a dayboat with a forward dining area and extended awnings, a sport fishing boat by integrating a full cabin for the helm console or even as a weekend boat by closing the forward deck. The prototype has two Hamilton waterjets run by two Yanmar 4LV250 inboard engines capable of a top speed above 40 knots, but other propulsion systems such as straight shaft, Z drives and outboards can also be mounted. In an interesting shift, new clients are also interested in solar powered and electric versions of the tender.
“The attention to detail that has gone into our first tender has been incredible and we are proud of the finish,” Branagh concludes. “The client and the crew love both the ergonomic styling of the boat and the performance it delivers, combined with an exceptionally stable ride. We are confident we can appeal to both the superyacht and the dayboat tender markets, as the combination of unique technology, innovation and functionality is what really sets Linx Tenders apart from the crowd.”
Related Content
Welding is not bonding
Discussion of the issues in our understanding of thermoplastic composite welded structures and certification of the latest materials and welding technologies for future airframes.
Read MorePlant tour: Teijin Carbon America Inc., Greenwood, S.C., U.S.
In 2018, Teijin broke ground on a facility that is reportedly the largest capacity carbon fiber line currently in existence. The line has been fully functional for nearly two years and has plenty of room for expansion.
Read MorePEEK vs. PEKK vs. PAEK and continuous compression molding
Suppliers of thermoplastics and carbon fiber chime in regarding PEEK vs. PEKK, and now PAEK, as well as in-situ consolidation — the supply chain for thermoplastic tape composites continues to evolve.
Read MorePlant tour: Albany Engineered Composites, Rochester, N.H., U.S.
Efficient, high-quality, well-controlled composites manufacturing at volume is the mantra for this 3D weaving specialist.
Read MoreRead Next
RS Electric Boats moves to larger facility, expands team
In response to demand for its newly launched composites intensive Pulse 63 electric RIB, the company announces continuing growth.
Read MoreHAV Group receives preliminary approval for hydrogen-based energy system for ships
Norwegian Maritime Authority approves LH2 tank design under the FreeCO2ast project, paving the way for commercialization of the zero-emissions marine system.
Read More“Structured air” TPS safeguards composite structures
Powered by an 85% air/15% pure polyimide aerogel, Blueshift’s novel material system protects structures during transient thermal events from -200°C to beyond 2400°C for rockets, battery boxes and more.
Read More