BMW i develops first electrified wingsuit for human flight
Embodying a futuristic approach, the carbon fiber and aluminum wingsuit with its electric propulsion system is a concept that even airsports daredevils won’t be able to ignore.

Photo Credit: Globetrender
Note: This article was provided by Globetrender, and originally reported by Erica Jamieson.
Together with BMW Group company Designworks (Newbury Park, Calif., U.S.) and air sportsman and professional base jumper Peter Salzmann, BMW i (a sub-brand of BMW founded in 2011 to design and manufacture plug-in electric vehicles) has developed an electric-powered wingsuit, which has been successfully flown over mountains in Austria. After jumping from a helicopter 3,000 meters up, Salzmann completed what is said to be the world’s first human flight powered by electric wingsuit in Nov. 2020. The wingsuit design even incorporates carbon fiber and aluminum.
The suit, propelled by two 13-centimeter carbon impellers with an overall output of 15 kilowatts (kW), allowed Salzmann to gain altitude and soar above the “Three Brothers” mountain peak in Austria. Mid-flight, the suit reached a top speed of 186 miles per hour. For a sport that typically celebrates top horizontal speeds of about 60 miles per hour, the “electrified wingsuit,” according to BMW i, will create new opportunities in daredevil airsports — and “Pay for Peril” adventure tourism.
“At the time, I was developing suits for skydiving and basejumping with a friend and basejumping mentor,” Salzmann tells BMW. “One of them was a supporting motor — and it’s an idea I just couldn’t shake. I found the idea of being able to jump from my local mountain wearing the wingsuit and land in my garden fascinating.”
Salzmann brought the concept to BMW and, in 2017, they got to work.
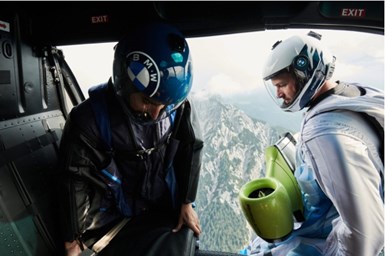
Photo Credit: Globetrender
“Our future-oriented approach with electric propulsion systems and innovative materials and technologies were a perfect fit for Peter Salzmann’s unusual but fascinating idea,” says Stefan Ponikva, vice president of brand experience at BMW i. “In my opinion, Peter Salzmann perfectly embodies the attitude of the BMW i brand with his vision, his passion and his courage. I was also impressed by his physical effort, combined with in-depth technical knowledge and a very clear understanding of the brand.”
Resembling “a futuristic mini-submarine,” the final design, in addition to using carbon fiber, also has a thumb and finger-operated throttle on the left sleeve. The electric propulsion system is powered by a 50-volt (V) lithium battery attached to the suit’s chestplate, and can produce thrust for up to 15 minutes. In alignment with the BMW i brand, the automaker’s line of fully electric cars, the wingsuit can be fueled by renewable energy.
“Sustainability is very important to me, and something I try to live my everyday life by. I enjoy nature from the air and on the ground — that’s why I aim to consistently follow the path of sustainability even when it comes to mobility,” Salzmann tells BMW.
The suit was tested in BMW’s horizontal wind tunnel, AEROLAB, and in a vertical wind tunnel in Sweden. An initial design prototype, with 40% additional power output was scrapped in favor of lighter design and improved freedom of movement.
The electric wingsuit was originally slated to debut in South Korea in spring 2020, a plan delayed by the pandemic. The Drei Brüder, or “Three Brothers” peaks in the Hohe Tauern Austrian mountain range, close to Salzmann’s childhood home, were selected as a replacement location.
To prepare for the flight, Salzmann completed specialized training to develop his core, neck and shoulder muscles in order to hold himself in the right position for the duration of the flight. With the first flight under his belt, Salzmann has already set his eyes on new goals — flying between high rise buildings in South Korea.
The maiden voyage has also marked the first edition of BMW’s #NEXTGen 2020 series, showcasing new technologies and vehicles that envision next-generation mobility.
Find the full report by Globetrender here.
Related Content
The lessons behind OceanGate
Carbon fiber composites faced much criticism in the wake of the OceanGate submersible accident. CW’s publisher Jeff Sloan explains that it’s not that simple.
Read MoreCryo-compressed hydrogen, the best solution for storage and refueling stations?
Cryomotive’s CRYOGAS solution claims the highest storage density, lowest refueling cost and widest operating range without H2 losses while using one-fifth the carbon fiber required in compressed gas tanks.
Read MorePlant tour: Teijin Carbon America Inc., Greenwood, S.C., U.S.
In 2018, Teijin broke ground on a facility that is reportedly the largest capacity carbon fiber line currently in existence. The line has been fully functional for nearly two years and has plenty of room for expansion.
Read MoreComposites manufacturing for general aviation aircraft
General aviation, certified and experimental, has increasingly embraced composites over the decades, a path further driven by leveraged innovation in materials and processes and the evolving AAM market.
Read MoreRead Next
VIDEO: High-volume processing for fiberglass components
Cannon Ergos, a company specializing in high-ton presses and equipment for composites fabrication and plastics processing, displayed automotive and industrial components at CAMX 2024.
Read MoreAll-recycled, needle-punched nonwoven CFRP slashes carbon footprint of Formula 2 seat
Dallara and Tenowo collaborate to produce a race-ready Formula 2 seat using recycled carbon fiber, reducing CO2 emissions by 97.5% compared to virgin materials.
Read MoreDeveloping bonded composite repair for ships, offshore units
Bureau Veritas and industry partners issue guidelines and pave the way for certification via StrengthBond Offshore project.
Read More