Hengshen to produce rear pressure bulkhead demonstrators
China-based Hengshen Carbon and Composites will produce five 4.5-meter demonstrator composite rear pressure bulkheads (RPB) for a Chinese aerospace OEM.
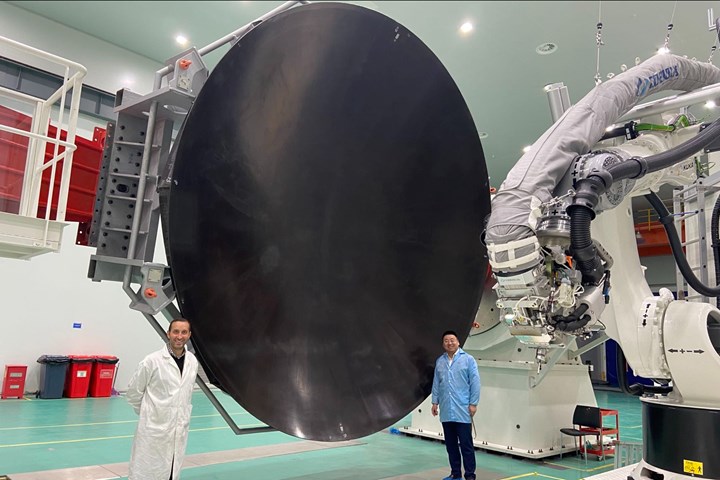
Hengshen rear pressure bulkhead tool, with Coriolis AFP system mounted on KUKA six-axis robot. Photo Credit: Hengshen
Carbon fiber manufacturer, fabrics, resins, prepreg producer and aerospace composite parts fabricator Hengshen Carbon and Composites. (Danyang, Jiangsu, China) reports that it has been engaged to produce five 4.5-meter full-scale demonstrator composite rear pressure bulkheads (RPB) for a Chinese aerospace OEM.
Simon Qian, managing director at Hengshen, says the project is designed to prove the manufacturing capabilities of the company to the OEM, as well as the capabilities of the material both for the layup tooling and the RPB product.
Two of the five RPBs will be fabricated using Hengshen’s own aerospace-grade toughened epoxy prepreg system, EH918, reinforced with the company’s intermediate modulus (IM) carbon fiber, HF40C. The other three RPBs will be fabricated using Solvay Composite Materials’ (Alpharetta, Ga., U.S.) CYCOM X850 toughened epoxy prepreg.

Hengshen RPB tool. Photo Credit: Hengshen
Anthony Ferronato, engineering director at Hengshen says both versions of the RPB will be fabricated using automated fiber placement (AFP) performed by a Coriolis (Queven, France) AFP system. OML tooling for the RPBs was fabricated by a French toolmaker, Loiretech Ingenierie (Nantes, France) using Hengshen’s tooling prepreg system, EH201.
The RPB tool has been specifically designed to use a carbon fiber layup surface reinforced with carbon fiber ribs. The layup surface is then mounted to a steel structure for overall stability and connection to the AFP machine. Loiretech used its proprietary technology to assemble the composite skin to the steel frame, which accounts for the thermal expansion variations between the composite skin and metallic frame during cure.
Hengshen says the main advantage with a composite tool is that it reduces the overall weight of the tool compared to conventional materials such as Invar or steel. This weight saving allows for a smoother operation during AFP layup without risk of having to overcome rotations of a heavier tool. Additionally, cure lead times are reduced as there is no need to heat the composite tool as is required with a metallic equivalent.
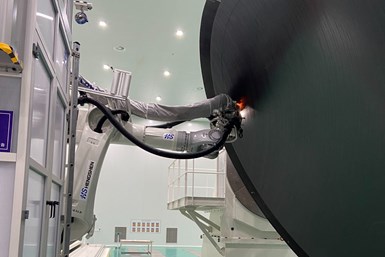
Coriolis AFP system lays up fiber on the Hengshen RPB mold. Photo Credit: Hengshen
Ferronato says the project required careful coordination between multiple organizations spread across the globe. “In a time of great uncertainty due to the current pandemic we have shown that the aviation industry can still thrive in the face of adversity,” he says.
After seven months of planning, engineering and manufacturing, the carbon fiber RPB tool arrived at Hengshen after a long journey from Nantes, France. The tooling was then checked for any damage or movement during transportation. In addition, a high-temperature vacuum trial was conducted on the tooling to ensure no air leaks. After successful trials, the tooling was transferred to the AFP machine room. The AFP machine room is an environmentally controlled space with a footprint of 800 square meters and houses the KUKA robotic AFP machine on rails, with two (20T and 40T) horizontal spindle axis positioners. The manufacturing envelope of the AFP machine is 20 x 6 meters, which easily accommodates the RPB.
The tooling was mounted on the Coriolis 40T AFP machine where final programming was undertaken prior to layup. The first product was manufactured using Hengshen’s EH918 toughened epoxy system, a co-bonded product of a dome shaped skin with omega-shaped core stringers. This was then followed by the production of the second product using Solvay’s X850 toughened epoxy prepreg. Both aerospace grade materials, X850 and EH918, were slit at Hengshen’s with a Mikrosam (Prilep, Macedonia) machine into AFP-grade 6.35-millimeter (0.25-inch) tapes.
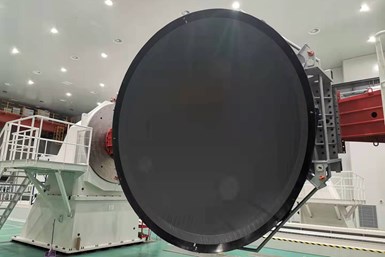
Fully laid up Hengshen RPB. Photo Credit: Hengshen
The curing process of the RPB is completed within Hengshen’s ASC Process Systems (Valencia, Calif., U.S.) autoclave. Cured products were then non-destructively tested before final machining is completed.
The RPBs will be delivered to the customer before the end of December 2021, after which the products will be mechanically tested in various forms to demonstrate compliance to the given loadcases and verification of the structural analysis. Assuming the RPBs pass these tests, the design, material, process and supplier (Hengshen) will be considered by the OEM for inclusion in emerging aircraft programs.
Related Content
Manufacturing the MFFD thermoplastic composite fuselage
Demonstrator’s upper, lower shells and assembly prove materials and new processes for lighter, cheaper and more sustainable high-rate future aircraft.
Read MoreA new era for ceramic matrix composites
CMC is expanding, with new fiber production in Europe, faster processes and higher temperature materials enabling applications for industry, hypersonics and New Space.
Read MoreComposites manufacturing for general aviation aircraft
General aviation, certified and experimental, has increasingly embraced composites over the decades, a path further driven by leveraged innovation in materials and processes and the evolving AAM market.
Read MoreWelding is not bonding
Discussion of the issues in our understanding of thermoplastic composite welded structures and certification of the latest materials and welding technologies for future airframes.
Read MoreRead Next
Automated aerocomposites production: Liquid molding or welded thermoplastic?
Two materials and process approaches are demonstrated for CFRP bulkhead production.
Read MoreVIDEO: High-volume processing for fiberglass components
Cannon Ergos, a company specializing in high-ton presses and equipment for composites fabrication and plastics processing, displayed automotive and industrial components at CAMX 2024.
Read MoreDeveloping bonded composite repair for ships, offshore units
Bureau Veritas and industry partners issue guidelines and pave the way for certification via StrengthBond Offshore project.
Read More