Inapal Plásticos manufactures SMC body panel for European SUV
A range of SMC components are being manufactured, from under hood to underbody and Class A components, and will provide the new luxury SUV with reduced part complexity and weight.
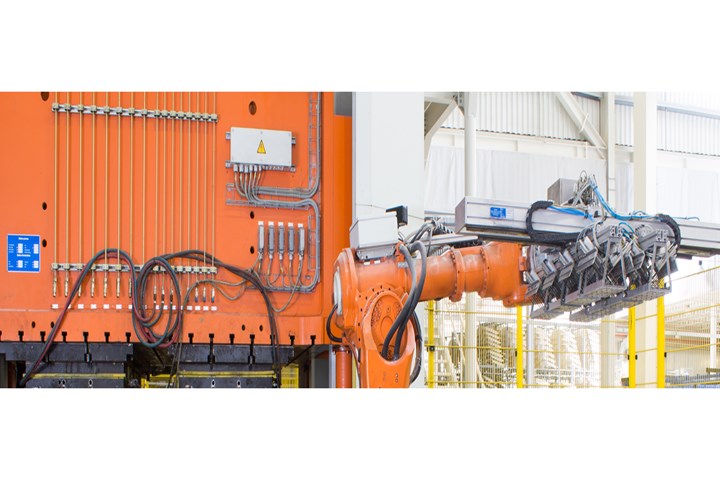
Photo Credit: Continental Structural Plastics
It was reported on Oct. 21 that Inapal Plásticos, Continental Structural Plastics’ (CSP, Auburn Hills, Mich., U.S.) operations in Portugal, will be manufacturing a number of lightweight, low-density sheet molded compound (SMC) components for a premium luxury auto maker’s first SUV. These 11 components, ranging from under hood to underbody and Class A components, will reportedly reduce part complexity and overall vehicle weight.
For example, molding the complex radiator assembly frame in a low-density composite material minimized the number of parts required under the hood. This reduced complexity, says CSP, since these parts, which are traditionally steel or aluminum, typically require multiple stamped components to be assembled to create the final product. Further, the SMC is said to have allowed for the molding of complex shapes and deep draws, enabling CSP to create a finished assembly that fit the dramatic and distinctive styling of the vehicle.
The vehicle’s tailgate, molded in low-density, Class A SMC, is complete after application of a conductive primer. This Class A SMC, says CSP, is e-coat oven capable, giving the customer the freedom to paint the tailgate in-house with the rest of the vehicle.
“Because this vehicle is the first SUV to be manufactured by this particular automaker, there are no direct comparisons to provide exact weight savings afforded by the use of low-density SMC,” says Orlando Rebelo, program manager at Inapal Plásticos. “But it is safe the say the weight savings will be significant and will contribute to the luxury performance customers will expect from this vehicle.”
The components will be manufactured at the CSP facilities in Leça, and Palmela, Portugal.
Related Content
-
Thermoplastic composites: Cracking the horizontal body panel nut
Versatile sandwich panel technology solves decades-long exterior automotive challenge.
-
Recycling hydrogen tanks to produce automotive structural components
Voith Composites and partners develop recycling solutions for hydrogen storage tanks and manufacturing methods to produce automotive parts from the recycled materials.
-
Jeep all-composite roof receivers achieve steel performance at low mass
Ultrashort carbon fiber/PPA replaces steel on rooftop brackets to hold Jeep soft tops, hardtops.