Leonardo produces two demonstrators for Clean Sky 2’s Composite Fuselage project
Full-scale structure and cabin interiors barrels prove out low-cost, lightweight composites plus innovative manufacturing, assembly and structural health monitoring.
Weight and cost reduction in the manufacturing processes and health monitoring of an aircraft fuselage are key to the competitiveness of Europe’s regional aircraft industry. Clean Sky’s Composite Fuselage project is pushing forward the technological frontiers for European aviation.
Clean Sky’s Composite Fuselage project, part of the Regional Aircraft Innovative Aircraft Demonstrator Platform (IADP), aims to develop technologies that are suitable for an advanced regional aircraft fuselage and to integrate and validate them up to full scale demonstrator level. The demonstrators — there are in fact two, one for the structure and one for the cabin interior — are being produced at Leonardo (Rome, Italy) in the form of full-scale fuselage barrels which are representative of a forward fuselage section, just aft of the aircraft cockpit.

The Composite Fuselage project focuses around innovative low cost and low weight composites, advanced manufacturing and assembling processes, and structural monitoring.
“Aircraft affordability is a critical parameter for regional airlines, and in the Composite Fuselage project, technology-wise, we are using a new approach, focusing on the materials and how to integrate all the fuselage’s design elements together with the new doors, new windows, frames and a new floor grid”
“Aircraft affordability is a critical parameter for regional airlines, and in the Composite Fuselage project, technology-wise, we are using a new approach, focusing on the materials and how to integrate all the fuselage’s design elements together with the new doors, new windows, frames and a new floor grid” says Ruud Den Boer, Project Officer at Clean Sky, adding that “production automation is also a very important parameter to support that, manifesting itself in such processes as automatic fiber placement and component integration.”
Maintainability is an important factor too, so integrated health monitoring – similar to what is available in road vehicles – is also a consideration within this project: ”We are using very small sensors which are integrated into the composite material which can monitor and measure the health of the fuselage, which will help predict when maintenance is required. Embedded sensors in the fuselage will also detect if there is an impact such as a bird-strike or interaction with debris on landings. All of this will lead to the reduction of maintenance costs when eventually used in a production aircraft. But for now, it is a technology development to assess if we can really produce this technology economically” says Den Boer.
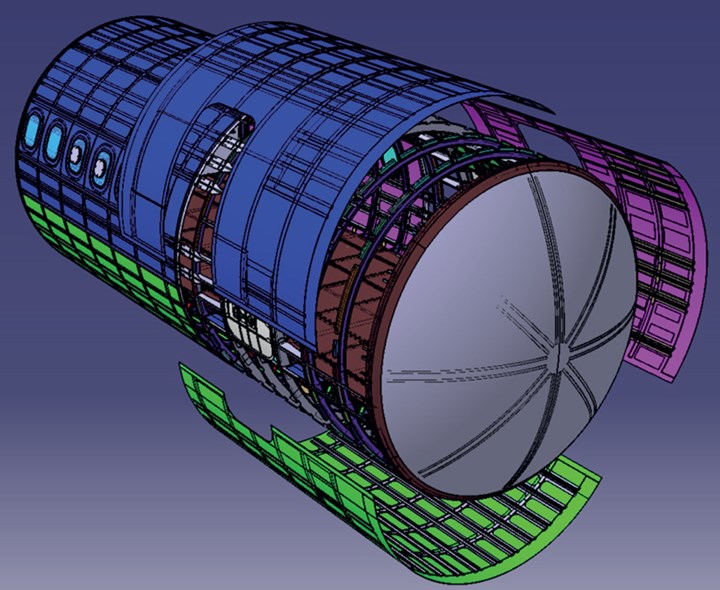
In the first quarter of 2018, the Preliminary Design Review of a fuselage structural demonstrator was successfully completed, leading to the completion of the preliminary design phase. The project is now in the detailed design phase, which will end in 2019 with the freezing of the fuselage component models in readiness for manufacturing to commence.
“Two full-scale fuselage demonstrators will be tested: the first one, the Structural Demonstrator, will be subjected to fatigue and static tests; the second one, the Passengers-Cabin Demonstrator, will assess vibro-acoustic, comfort, thermal tests and systems integration,” says Vittorio Ascione, who is responsible for Engineering/Structures Analysis and Methods at Leonardo.
“At the moment, tests on specimens, elements and sub-components have already been carried out, based on the application of the building block approach. And further results will be available through the full-scale demonstrations even if results coming from tests already performed on innovative composite specimens are being used for the design phases.”
“Structural weight and cost reduction goals in the Structural Demonstrator will contribute to reducing CO2 emissions, thanks to lighter structures and more automated and eco-compatible manufacturing and assembly processes.”
As for the social and environmental benefits, Ascione says that “structural weight and cost reduction goals in the Structural Demonstrator will contribute to reducing CO2 emissions, thanks to lighter structures and more automated and eco-compatible manufacturing and assembly processes. Increased comfort and wellbeing in the passenger cabin demonstrator will contribute to improving the passenger in-flight experience in advanced regional aircraft.”
By the end of the project, the structural behavior and the performance — in terms of internal noise reduction, passenger comfort and wellbeing — are scheduled to be evaluated through full-scale tests, which will be executed at Leonardo Aircraft Division and also at the Fraunhofer Institute.
Related Content
Recycling hydrogen tanks to produce automotive structural components
Voith Composites and partners develop recycling solutions for hydrogen storage tanks and manufacturing methods to produce automotive parts from the recycled materials.
Read MoreBio-based acrylonitrile for carbon fiber manufacture
The quest for a sustainable source of acrylonitrile for carbon fiber manufacture has made the leap from the lab to the market.
Read MoreNovel composite technology replaces welded joints in tubular structures
The Tree Composites TC-joint replaces traditional welding in jacket foundations for offshore wind turbine generator applications, advancing the world’s quest for fast, sustainable energy deployment.
Read MoreComposites end markets: Electronics (2024)
Increasingly, prototype and production-ready smart devices featuring thermoplastic composite cases and other components provide lightweight, optimized sustainable alternatives to metal.
Read MoreRead Next
Developing bonded composite repair for ships, offshore units
Bureau Veritas and industry partners issue guidelines and pave the way for certification via StrengthBond Offshore project.
Read More“Structured air” TPS safeguards composite structures
Powered by an 85% air/15% pure polyimide aerogel, Blueshift’s novel material system protects structures during transient thermal events from -200°C to beyond 2400°C for rockets, battery boxes and more.
Read MorePlant tour: Daher Shap’in TechCenter and composites production plant, Saint-Aignan-de-Grandlieu, France
Co-located R&D and production advance OOA thermosets, thermoplastics, welding, recycling and digital technologies for faster processing and certification of lighter, more sustainable composites.
Read More