Spirit AeroSystems enters five-year collaboration with Infosys
Infosys will provide aerostructures and systems engineering services for product development of aircraft programs and MRO services.
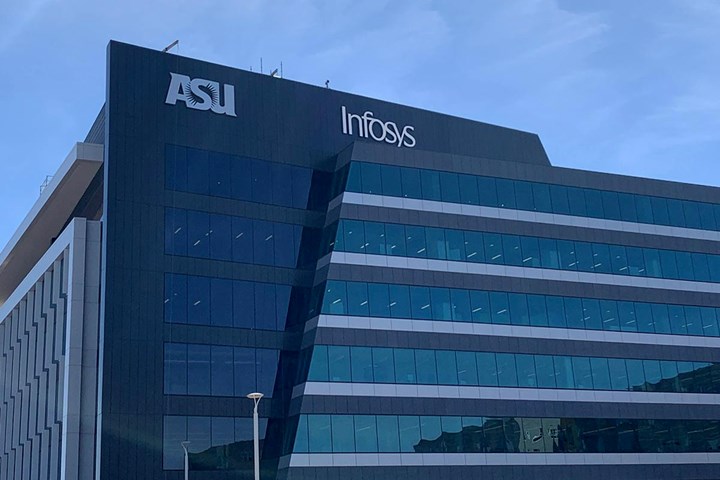
Photo Credit: Infosys
On Sept. 7, a five-year agreement was announced between aerostructures manufacturer Spirit AeroSystems Inc. (Wichita, Kan., U.S.) and digital services and consulting company Infosys (Bengalaru, India).
Through this collaboration, Infosys will provide aerostructures and systems engineering services to support the design and manufacture of Spirit’s composite and metallic structures, including new product development and maintenance, repair and overhaul (MRO) on composite components for engine nacelles, control surfaces and other parts.
The collaboration will extend to Spirit AeroSystems’ operations in Wichita; Belfast, Northern Ireland, U.K.; Prestwick, Scotland, U.K.; Kinston, N.C., U.S.; Tulsa, Okla., U.S.; and Dallas, Texas, U.S.
“Design for manufacturing is a key element of our engineering development work. We use engineering tools from customers which are state-of-the-art as well as those that are industry best-in-class. Additionally, Spirit has developed design automation, and analysis tools and methods, for both composite and metallic structures. Infosys will work alongside us, providing a complementary service, on the use of these advanced tools for developing and supporting certification of cost-competitive designs. In MRO, Infosys will provide design support for repair scenarios to rebuild parts to original capability,” explains Sean Black, senior VP and chief engineer, Engineering and Technology at Spirit AeroSystems.
According to Infosys, this strategic collaboration builds on 16 years of longstanding relationship between the two organizations, during which Infosys has provided innovative design solutions for some of Spirit’s aerostructure programs. As part of this engagement, Infosys will offer end-to-end product development services, including design engineering, sustaining engineering, systems engineering, stress engineering, manufacturing engineering, and repair and maintenance. Leveraging knowledge-based engineering and engineering automation, Infosys also aims to accelerate product development across the value stream. In addition, Infosys will support Spirit to secure highly efficient structural designs and a robust certification process, contributing to the manufacture of innovative, lightweight and more sustainable aircraft structures and components.
In addition, Infosys reports that its Aerospace Center of Excellence has a track record of world-class execution of design and engineering solutions for more than 22 years. With deep capabilities in aerostructure design spanning conceptualization to release, mature composite design and engineering automation, Infosys says it collaborates with seven of the top 10 global aerospace companies and has been recognized as a leading player in aerospace and defense manufacturing.
“At Spirit AeroSystems, we believe our ability to continuously advance our offering at design and engineering levels is one of our competitive differentiators. Our longstanding collaboration with Infosys means we are well-positioned to co-innovate on critical stages of product development, ensuring we continue to pursue the highest standards in quality and airworthiness,” says Black. “This strategic agreement further reinforces our strengths and will leverage mutual synergies to accelerate the development of world-class, sustainable aerostructures and services across our commercial and aftermarket business segments.”
“Now more than ever, aerospace and defense organizations need to rapidly reinvent their digital foundation,” Jasmeet Singh, executive VP and global head of manufacturing at Infosys, adds. “We are thrilled to deepen our strategic collaboration with Spirit AeroSystems and accelerate their digital transformation, by pushing the envelope in design and product engineering. With our investments in aerostructure engineering and next-gen technologies like artificial intelligence and cloud, we are confident of delivering compelling value to Spirit and take our collaboration to newer heights.”
Related Content
Cryo-compressed hydrogen, the best solution for storage and refueling stations?
Cryomotive’s CRYOGAS solution claims the highest storage density, lowest refueling cost and widest operating range without H2 losses while using one-fifth the carbon fiber required in compressed gas tanks.
Read MorePlant tour: Spirit AeroSystems, Belfast, Northern Ireland, U.K.
Purpose-built facility employs resin transfer infusion (RTI) and assembly technology to manufacture today’s composite A220 wings, and prepares for future new programs and production ramp-ups.
Read MoreNext-generation airship design enabled by modern composites
LTA Research’s proof-of-concept Pathfinder 1 modernizes a fully rigid airship design with a largely carbon fiber composite frame. R&D has already begun on higher volume, more automated manufacturing for the future.
Read MorePlant tour: Albany Engineered Composites, Rochester, N.H., U.S.
Efficient, high-quality, well-controlled composites manufacturing at volume is the mantra for this 3D weaving specialist.
Read MoreRead Next
Sierra Space, Spirit AeroSystems aim to accelerate the commercialization of space
New, long-term agreement is to lower the cost of access to space, accelerate production of Shooting Star Cargo Modules as part of expanding Dream Chaser spaceplane franchise.
Read MoreHexcel joins collaboration program at Spirit’s Aerospace Innovation Centre
Collaborative activities include development of RTM production applications highlighting future opportunities for liquid composite molding.
Read MoreDeveloping bonded composite repair for ships, offshore units
Bureau Veritas and industry partners issue guidelines and pave the way for certification via StrengthBond Offshore project.
Read More