DC dielectric sensors for industrial composites production
Synthesites in situ process monitoring enables cure decisions based on real-time Tg evaluation that can reduce cure cycles by up to 50%.
Share

As manufacturers seek to simultaneously reduce cost and increase rate for composite parts production, the ability to see inside molding processes in real time and monitor resin flow, viscosity, temperature, pressure and Tg/state of cure becomes a differentiator. Synthesites (Uccle, Belgium) has developed this ability. Based on results reported by the German Aerospace Center (DLR, Stade) and the National Composites Centre (NCC, Bristol, U.K.), this technology has the potential to cut cycle times by up to 50%, with cure decisions based on Tg and degree of cure per resin and part vs. conservative time periods based on generic material studies. It is, in fact, progress toward Composites 4.0 production, using data from sensors to control processes and equipment, and also to improve simulation and design.
I first reported on Synthesites via the OPTO-Light project (see “Thermoplastic overmolded thermosets, 2-minute cycle, one cell”). In fact, the ability to join thermoplastics to thermosets in OPTO-Light without laser-ablated surfaces was made possible by using in-mold sensors for pressure, temperature, direct current resistivity (DCR) and dielectric analysis (DEA). The DCR sensors were supplied by Synthesites and those for DEA were supplied by Netzsch (Selb, Germany). Both are dielectric sensors which measure the resin’s electrical properties. I will discuss the history and differences in these technologies below.
The technology Synthesites has developed with a range of commercial customers is impressive, including industrial production of wind blades and the resin infused wings for the C-Series, now Airbus 220. It has also been demonstrated for a range of materials and processes, including autoclave-cured prepreg, resin infusion and high-pressure resin transfer molding (HP-RTM).

Synthesites’ selected list of commercial customers includes leading manufacturers of composite structures for aerospace, automotive and wind blades. SOURCE | Synthesites
Dielectric analysis (DEA), AC vs. DC
DEA has been used for decades to monitor viscosity and cure state changes in thermoset and thermoplastic resins, adhesives and paints. DEA can be used to analyze cure in composites by applying a voltage between two electrodes placed in contact with the matrix resin. The voltage may be alternating current (AC) or direct current (DC).
Use of AC applies a sinusoidal, time-varying voltage at frequencies between 0.1 Hz and 100 kHz to one electrode. This causes a signal of the same frequency to be induced in the second electrode. The change in the amplitude and phase angle shift in the signal relative to the applied voltage (see figure below) are measured and used to calculate the resin’s dielectric properties, including the dielectric constant (permittivity), dielectric loss factor, ion conductivity and ion viscosity (electrical resistivity). From ion viscosity, resin viscosity can be calculated.
As the resin changes from a liquid to a solid, the amount and mobility of charged ions will decrease due to the growing molecular network. This can be seen in dielectric sensor measurements, which reflect the resin’s ion conductivity (charged ions will move toward the electrode of opposite charge) and dielectrical polarization (dipoles will orient with the electric field).

DEA applies an excitation voltage and measures the change in amplitude and phase angle shift of the induced signal/response (left). These measurements will change as a resin changes from liquid to solid due to ion mobility toward the opposite-charge electrode (ion conductivity) and polarization as dipoles orient with the electric field (right). SOURCE | Netzsch Thermal Academy
Ion conductivity is inversely related to resin viscosity prior to gelation and to rigidity after gelation (high ion mobility, low resin viscosity and low rigidity). The inverse of ion conductivity, resistivity, is thus directly related to viscosity/rigidity changes in the matrix resin.
Increase in resistivity has been shown to correlate with increase in Tg. This is the basis of direct current resistivity (DCR), which is just DEA using direct current (DC), and the description initially given to the process Synthesites developed.
As explained above, this technique of using DC voltage for DEA is based on correlations between resistivity and state of cure. These were reported in 1962 by R.W. Warfield in “Properties of Crosslinked Polymers as Evidenced by Electrical Resistivity Measurements”, Makromoleculare Chemistry, Vol. 58. (See bottom for references used in this section.)
History of DEA and AC vs. DC sensors
This history, published by Lambient Technologies LLC (Cambridge, Mass., U.S.), confirms decades of evolution in DEA and the development of AC sensors from MIT to Netzsch and Lambient.
SOURCE | https://lambient.com/history
“The idea of cure monitoring is quite old,” explains Dr. Nikos Pantelelis,director of Synthesites. “In the 1980s, the method of dielectric sensing was considered more mature than others, such as optical fibers. MIT (Massachusetts Institute of Technology) worked on it and tried to implement it in production. This technology is what Netzsch bought and uses today.”
Synthesites was established in 2008. “We developed our technology from scratch using electric sensors with direct current, not alternating current,” Pantelelis relates. “For us, the drawback with using conventional AC dielectric sensors is the requirement to excite the resin at a range of frequencies and then measure the impedance response for various signals. It’s not only challenging to process all of this data, but as the resin changes from liquid to solid, you need to focus on different signal frequencies in order to obtain the right information.”
Pantelelis says that Synthesites DC sensors can measure very low conductivity and high resistivity, “which is necessary to measure the transformation of resins during cure.” He asserts that using conventional DEA at only one frequency to make it simpler does not give accurate data. “We don’t have multiple frequencies but simply apply a constant voltage. The downside is that this approach is very narrow, meaning it works well for very specific applications such as resin curing but not for everything. However, when comparing the performance of our equipment to conventional DEA, ours can measure the whole range of curing even at lower temperatures. Companies supplying instruments and services outside of composites don’t like our approach because it has limited parameters to tune.”
This isn’t a problem for Synthesites because it has specifically targeted composites. “Our approach works well across a wide range of composite resins and processes, including thermosets, RTM, prepreg and even reactive thermoplastics like Elium.” (Elium is the low-viscosity thermoplastic from Arkema (Colombes, France) that can be processed using resin infusion.)
Synthesites DC dielectric sensors (top left) were used to monitor cure in the RECOTRANS project exploring microwave cure (note mw6 and mw7 in table) of Elium liquid thermoplastic resin. SOURCE | Synthesites
If DEA using DC was known in the 1960s, then why were AC sensors favored in the 1980s and moving forward? “Thirty years ago, the technology for DEA using DC sensors was not so developed,” Pantelelis points out. “But we have advanced our approach to deliver very smooth and accurate measurements for industrial production. We have demonstrated and continued to develop our systems with customers like GE Aviation (Batesville and Ellisville, Miss., U.S.) and Bombardier who are processing large parts with liquid resin molding. Our systems are also used every day in wind blade production and have demonstrated the ability for industrial production of autoclave-cured prepreg laminates.”
Process control
Pantelelis explains how Synthesites DC sensors are just one part of an integrated system to monitor composites processing and cure. “We directly measure resistance and temperature, and from this we calculate online viscosity, degree of gelation and degree of cure. We use durable in-mold sensors but also gate sensors and in-line sensors for resin inlets, outlets and feed lines, as well as disposable sensors on parts. You use the sensors only where you need them.”
The temperature sensors are platinum resistance temperature detectors (RTDs), which offer much higher accuracy (within 0.1°C) than thermocouples as well as stability for years versus the measurement drift possible with thermocouples. RTDs are standard equipment in many industrial applications. Gate sensors (see process control diagram below) are binary, reporting resin flow as on or off, although there is a second version that can also report viscosity. Synthesites has developed sensors for use with carbon fiber without risk of galvanic corrosion, sensors that can be used through a vacuum bag and shaped in-mold sensors to match mold geometry.
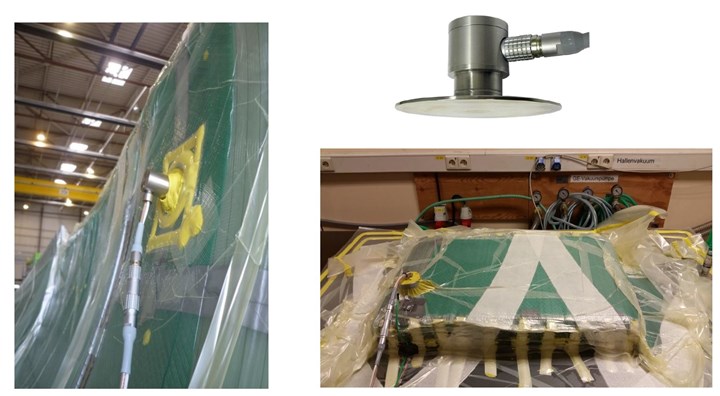
Synthesites has developed a DC dielectric sensor for cure monitoring of vacuum-bagged composite laminates in wind blade production. SOURCE | Synthesites
The next components are OPTIFLOW and OPTIMOLD data acquisition units. OPTIFLOW provides in situ, real time monitoring of resin arrival and temperature for liquid composites molding. It verifies and logs resin flow and can identify production deviations during resin infiltration. OPTIMOLD uses temperature and resin resistance measurements to make calculations and monitor the state of the resin including mix ratio, chemical aging, viscosity, Tg and degree of cure. It can be used with prepreg and liquid molding processes.

Synthesites process control systems integrate sensors, OPTIFLOW and/or OPTIMOLD data acquisition units and OptiView and/or Online Resin State (ORS) software. SOURCE | Synthesites, edited by CW
OPTIFLOW and OPTIMOLD units are controlled by OPTIVIEW software. “This software provides data acquisition and storage and is provided free of charge with our equipment,” Pantelelis explains. “We also offer Online Resin State (ORS) software, a more advanced option which customers can purchase extra. It collects input, makes online calculations and sends output for intelligent process control.”
Both OPTIFLOW and OPTIMOLD systems continuously check to make sure sensors are connected and readings are within range. “When you are relying on these sensors for process control, it is imperative that the systems alarm if a sensor is not working or if its readings are beyond prescribed limits,” says Pantelelis. Both systems also have relay outputs for controlling process equipment. For example, feed line valves can be open or closed based on resin arrival data, and heating/cooling equipment can be managed based on resin viscosity. “You can feed output from pressure sensors into OPTIMOLD,” notes Pantelelis, “and thus control pressure in the mold based on viscosity data.”
Measurements and typical data curves
The screenshots below show OPTIMOLD measurements from high-pressure compression RTM (HP-CRTM) trials at NCC (Bristol, U.K.). The first set, from a simple trial at 115°C, shows how real-time measurements of resin electrical resistance and temperature are converted into estimated viscosity and Tg by ORS software.
SOURCE | “Online Viscosity and Tg Measurement of CFRP manufactured using High-Pressure RTM” by Nikos Pantelelis, Matt Etchells and Cristian Lira (NCC Bristol, U.K.), et. al., SAMPE Europe Conference 2019 Nantes.
In the graphs below, electrical resistance and temperature (top graphs) were recorded at 110° (left) and 120°C (right). Below the resistance (R) and temperature (T) readings are the graphs showing calculated viscosity and Tg at 110°C (left) and 120°C (right). These measurements were from two OPTIMOLD sensors located in the upper mold half (Sn.1 and Sn.2, bottom photo) while cavity pressure was recorded using two Kistler 6162A pressure sensors (Sn.3 and Sn.4).
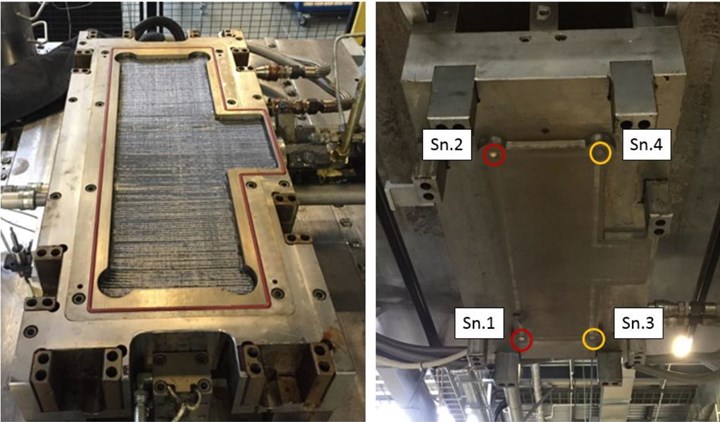
SOURCE | “Cure Monitoring of Highly Reactive Resin During High-Pressure Compression Resin Transfer Moulding” by M. Etchells, N.Pantelelis and C. Lira, 18th European Conference on Composite Materials (ECCM18, June 2018, Athens, Greece).
All data recorded by the in-mold sensors as well as the press and injection equipment can be collated into a single log file, allowing a detailed image of the manufacturing process for each component created.
Reducing cure time
“We have the potential to drop cure time by more than 30% because the manufacturer can see the Tg in real time, so they can decide when to stop the cure cycle,” Pantelelis explains. “They don’t have to wait to complete a longer than necessary legacy cycle. For example, the legacy cycle for RTM6 is 2 hours at 180°C for full cure. We’ve seen that in certain geometries this can go down to 70 minutes.”
The goal then, is to stop the process once cure is complete? “It’s not about full cure but attaining the level of cure that each component needs,” says Pantelelis. “Full cure takes too long. The key is being able to see when sufficient cure is reached. Wind blade manufacturers have a target Tg. When they reach that, they can start cooling. So the need is a sensor that can give very accurate measurements of Tg in real-time.”
Synthesites completed a demonstration project with Hutchinson (Paris, France) to produce an automotive suspension blade made with glass fiber/epoxy and RTM for the EU-funded ECOMISE project (Enabling Next Generation COmposite Manufacturing by In-Situ Structural Evaluation and Process Adjustment, 2013-2016). The goal of this project was to optimize the RTM cycle based on real-time process monitoring:
- The first heating ramp would be triggered by completion of resin infiltration based on sensors.
- The second heating ramp would be triggered by completion of cure based on Tg calculation.
- Cooling would be triggered by completion of the post-cure based on Tg calculation.
The Synthesites system comprised two (2) in-mold sensors for cure (CS1, CS2), one (1) in-mold sensor for resin flow and temperature (Flow Sensor 1) and eight (8) disposable sensors for resin flow/temperature — four (4) embedded into the test part and four (4) attached to the tool surface.


This OPTIVIEW screen shot shows resin resistance and temperature measurements from the in-mold Cure sensor 1 (CS1) and Cure sensor 2 (CS2) in the lower half of the RTM mold. SOURCE | “Towards the intelligent RTM system” by Antonios Tontisakis, CAMX 2016.
“OPTIMOLD and OPTIFLOW units can be connected together through ethernet so that all sensors can be recorded in one Optiview session,” Pantelelis explains. “Thus, CS1 and CS2 were connected to two OPTIMOLD units, the in-mold flow sensor 1 and the eight disposable flow sensors were connected to three OPTIFLOW units.”
This system of sensors, OPTIMOLD/OPTIFLOW data acquisition units and OPPTIVIEW/ORS software was then applied during RTM molding trials to establish targets for various process stages, including resin injection/infiltration and two Tg targets. “This was a thick part made using unidirectional fiber and Huntsman epoxy resin,” says Pantelelis. “In this case, we used flow wire sensors to check flow within these UD plies, which are typically tightly packed and can create challenges during resin infiltration.”
In the OPTIVIEW software, measurements from the two sets of disposable resin flow sensors turn from green to yellow once resin arrives at that sensor. These measurements would signal end of resin infiltration and trigger first heat ramp to 90°C for cure. SOURCE | CAMX 2016

RTM tool for Hutchinson composite suspension blade with OPTIMOLD and OPTIFLOW units stacked behind the control laptop running OPTIVIEW and ORS software. SOURCE | “Towards the intelligent RTM system” by Antonios Tontisakis, CAMX 2016.

Temperature (TC1, TC2) and resistance measurements from in-mold Cure sensors 1 and 2 were used to calculate Tg (TgR1, TgR2) which is graphed against theoretical Tg based on kinetic models (TgK1, TgK2). From this, the first target Tg (90°C) and second target Tg (130°C) were established. SOURCE | CAMX 2016.
RTM process control based on sensor measurements. (1) Flow sensors signal completion of resin infiltration and trigger first ramp to 90°C cure. (2) When calculated Tg from cure sensor measurements reaches first target Tg, it signals completion of cure and triggers second ramp to 130°C post-cure. (3) When calculated Tg reaches second target Tg, it signals completion of post-cure and triggers cooling/demolding. SOURCE | CAMX 2016, edited by CW.
Using this process control system, the ECOMISE project at Hutchinson was able to reduce the cure cycle by more than 30%.

The optimized process using Synthesites cure monitoring and real-time resin state process control cut cycle time by more than 30% for the Hutchinson RTM composite suspension blade in ECOMISE. SOURCE | CAMX 2016.
Calibration
Calibration is required for online Tg monitoring. As measurements are collected from the sensors via OPTIMOLD units, the ORS software translates these into viscosity and Tg based on the calibration for that specific resin. “This calibration is work done ahead of processing to provide the correlations that the ORS software will use for its calculations,” Pantelelis explains. “We calibrate by placing the resin in a rheometer and measuring temperature and viscosity. By applying the appropriate formulas, you then calculate corresponding resistance and Tg. We develop calibration of resins for our customers based on their standards, and study the resin’s different cure cycles. This calibration data is then used by the ORS software whenever processing that resin.”

Results of trials by Carbon Rotec showing accuracy of Tg calculated by ORS software compared to DSC testing. SOURCE | Synthesites, published in SAMPE Journal, v. 53/6, Nov/Dec 2017, pp. 6-10.
The accuracy of the ORS software’s real-time Tg calculations was shown in trials by wind blade producer Carbon Rotec Composite Technology (Lemwerder, Germany). Tg calculated online by the ORS software was compared with Tg measured right after demolding by performing Differential Scanning Calorimeter (DSC). For isothermal processing, the mean difference was 1.61°C and for non-isothermal processing, it was 2.15°C.
“This accuracy has been repeatedly shown in private projects with other customers,” says Pantelelis.
Advances for industrial production
This sensor- and data-driven process control is indeed a great step toward fully automated and intelligent Composites 4.0 manufacturing. Although it has been demonstrated in ECOMISE and also with the NCC in Bristol, it is not yet being used in everyday production. “The idea of using the sensors to see Tg and then start cooling has indeed been started in wind blade manufacturing,” Pantelelis reports, “but it is not yet fully automated. The system alarms when the target Tg is reached and then the operator stops the cure cycle. The automation is straightforward, and will be completed once the manufacturer has validated the system's accuracy during the pilot phase.”
“Toward this target, we have developed a new workstation to allow the production operator to oversee the automated process, which requires no input from his side,” he continues. “We have seen in the manufacturing of wind turbine blades that using a single workstation during resin and adhesive curing can shorten cycle time by at least 2-3 hours without sacrificing quality.”
Although Bombardier Belfast, now Spirit AeroSystems, does use Synthesites equipment in the production of its resin infused composite wing for the C-Series, now Airbus A220, the process control is not automated. However, Synthesites also worked with Bombardier in ECOMISE, and that development is being carried forward. One key achievement was sensors that feed through the autoclave wall. As explained in my 2013 blog, “C-Series composite wing”:
Bombardier is injecting after the layup has been placed in its 21.3m long by 5.6m diameter autoclave, enabling temperature and pressure to be maintained at the level required for reduced viscosity and wetout — Cytec 890 is injectable at 80˚C . . . After resin injection is complete, positive pressure is applied in the autoclave during consolidation, causing the tooling elements to close, compact the wet laminate and eject excess resin back out of the resin inlet into a specifically designed resin dump.
The demonstrator at Bombardier (top) and an equivalent system (monitoring systems, wiring and sensors) developed for an R&D autoclave (bottom). SOURCE | “Intelligent process monitoring and control: Two industrial applications” by Nikos Pantelelis, et. al., International Conference on Manufacturing of Advanced Composites (ICMAC 2015, Bristol, UK).
“Like most manufacturers in commercial aerospace, it is interested to ensure quality and increase rate,” explains Pantelelis. The layout below and results from ECOMISE were for a demonstrator, not a commercial part. It used two OPTIMOLD units with two in-mold cure sensors and three OPTIFLOW units with four in-mold flow sensors and four inline sensors at the vacuum lines. “OPTIFLOW can monitor up to four resin arrival and four temperature/resistance sensors,” Pantelelis notes. “The targets of the demonstration were fully achieved. We proved that the sensors, wiring and systems can work without any problem under the most challenging aerospace specifications. It was interesting that the resin arrival measurements showed large differences compared with the flow simulations. Also, the online Tg monitoring showed that the cure cycle followed for that specific demonstrator could have been significantly shorter.”
“Manufacturers are looking to get more insight into what is happening exactly during molding and how they can stabilize and optimize their processes.”
“We are now developing a monitoring system for the bondlines,” says Pantelelis, “primarily for wind turbine blade production but ultimately for any bonding process. Although we are currently very busy with the wind turbine industry, which is trying to reduce costs, we see more and more interest from the aerospace sector as it moves toward liquid composite molding for mass production. Manufacturers are looking to get more insight into what is happening exactly during molding and how they can stabilize and optimize their processes.”
Ecomise and Recotrans projects received funding from the European Union’s FP7 and Horizon 2020 Research and Innovation Programmes under Grant Agreement nº NMP2-SL-2013-608667 and 768737, resp.
References for the section “Dielectric analysis (DEA), AC vs. DC” include:
- “Real-time UV cure monitoring” by VINCENTZ, published in European Coatings Journal, issue 11/2003, p. 7.
- “Online Process Monitoring Systems – Benchmark and Test Study” by Reinhold Meier1, Swen Zaremba1, Florian Springl1, Klaus Drechsler1, Fabrice Gaille2 and Christian Weimer2 — 1 Institute for Carbon Composites, TU Munich, Garching, Germany. 2Eurocopter Deutschland GmbH, Donauwörth. Flow Process in Composite Materials – FPCM 11, July 9-12, 2012, Auckland, New Zealand.
- Nondestructive Characterization of Materials VIII edited by Robert E. Green, Proceedings of the 8th Intl. Symposium on Nondestructive Characterization of Materials, June 16-20, 1997, Boulder, Colorado, U.S., published by Springer Science & Business Media, pp. 384-385.
Another helpful reference is “The Handbook of Dielectric Analysis and Cure Monitoring” by Huan L. Lee, published by Lambient Technologies.
Related Content
Combining multifunctional thermoplastic composites, additive manufacturing for next-gen airframe structures
The DOMMINIO project combines AFP with 3D printed gyroid cores, embedded SHM sensors and smart materials for induction-driven disassembly of parts at end of life.
Read MoreThe potential for thermoplastic composite nacelles
Collins Aerospace draws on global team, decades of experience to demonstrate large, curved AFP and welded structures for the next generation of aircraft.
Read MorePlant tour: Joby Aviation, Marina, Calif., U.S.
As the advanced air mobility market begins to take shape, market leader Joby Aviation works to industrialize composites manufacturing for its first-generation, composites-intensive, all-electric air taxi.
Read MorePEEK vs. PEKK vs. PAEK and continuous compression molding
Suppliers of thermoplastics and carbon fiber chime in regarding PEEK vs. PEKK, and now PAEK, as well as in-situ consolidation — the supply chain for thermoplastic tape composites continues to evolve.
Read MoreRead Next
Advancing thermoplastic composites and RTM for Clean Sky 2 in Spain
EURECAT leads projects for TPC keel beam, window frames and thermoset RTM fuselage frames with TPC shear ties for next-gen aircraft.
Read MoreDeveloping bonded composite repair for ships, offshore units
Bureau Veritas and industry partners issue guidelines and pave the way for certification via StrengthBond Offshore project.
Read MorePlant tour: Daher Shap’in TechCenter and composites production plant, Saint-Aignan-de-Grandlieu, France
Co-located R&D and production advance OOA thermosets, thermoplastics, welding, recycling and digital technologies for faster processing and certification of lighter, more sustainable composites.
Read More