EconCore, Solarge launch lightweight, sustainable solar panel
Netherlands-based EconCore and Solarge have collaborated to develop a composite solar panel that offers weight savings of up to 65%.
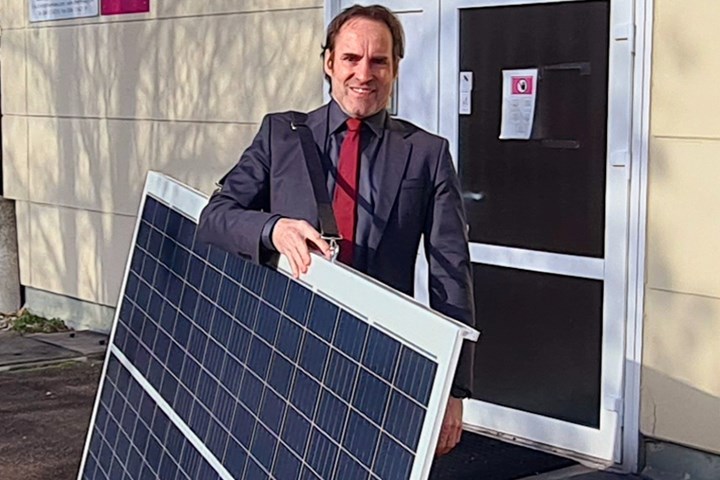
EconCore/Solarge composite solar panel. Photo Credit: EconCore
EconCore (Leuven, Netherlands), a manufacturer of honeycomb sandwich material production technology, and Solarge (Weert, Netherlands), a producer of lightweight, sustainable solar panels, are launching at JEC World 2023 a new lightweight, fully circular solar panel, reducing the weight of solar installations by up to 65% for rooftops.
Since early 2018, EconCore and Solarge have intensively collaborated to develop this next-generation solar panel, removing weight by replacing heavy glass with lightweight honeycomb materials. The result is a fully recyclable alternative to more traditional non-sustainable materials. A new EconCore/Solarge panel that measures just over 2.66m2 weighs 14.5 kg, compared to more than 28 kg with the old glass-type model.
The companies are looking at how to replace glass traditionally used in solar panels with a composite, honeycomb structure and a polymer frontside. Honeycomb has fantastic mechanical properties, being very strong and very rigid for a given weight or density. Glass panels also need an aluminium frame, and again honeycomb obviates this, removing yet more weight.
Rigidity and impact resistance are both important properties for solar panels; as bending and impact, for example of hail stones, can result in breakages or decreased efficiency. The honeycomb panels can handle these stresses in different ways, not just through being more rigid.
The new Solarge circular panels enable improved resistance against UV radiation and has much better heat conductivity than glass panels. Solar panels are less efficient as temperature increases and honeycomb delivers a more effective means of controlling temperature.
Finally, current panels are very difficult to recycle, whereas EconCore has recently developed a honeycomb core made from recycled materials. One of the possible designs focuses on a monomaterial solution where only the solar cells and the encapsulant would be a different material. And with the encapsulant material being thermoplastic, this would allow the splitting and sorting of the different constituents.
This development builds on Solarge’s traditional strength in sustainability with:
- Ultra-low carbon solar footprint: 25% better than conventional modules (in new factory);
- Reduction of material resources need to deliver the mechanical performance;
- 100% recyclability;
- Elimination of toxic materials such as PFAS.
Tomasz Czarnecki, COO at EconCore, says, “Solar power is an important mechanism to strip carbon out of energy production. It’s a simple equation – the more solar panels we can deploy, the more solar energy we can harness, the greater the protection against climate change.
“Making photo voltaics lighter, cheaper, and more efficient means many more buildings will be able to be harnessed to produce solar energy, and every roof that is limited by weight will be able to take more panels. And these panels are sustainable – this has huge potential in the battle against climate change.”
Huib van den Heuvel, CCO at Solarge, adds, “We see a huge potential in rooftop application in the commercial and industrial building segment and the agricultural sector for lightweight solar panels, all over the world. Compared to glass based solar panels the production of this composite product is very easily scalable. We value the collaboration with ThermHex Waben (EconCore) as a manufacturing partner that supports our ambitious growth plans.”
Related Content
Recycling end-of-life composite parts: New methods, markets
From infrastructure solutions to consumer products, Polish recycler Anmet and Netherlands-based researchers are developing new methods for repurposing wind turbine blades and other composite parts.
Read MorePlant tour: Albany Engineered Composites, Rochester, N.H., U.S.
Efficient, high-quality, well-controlled composites manufacturing at volume is the mantra for this 3D weaving specialist.
Read MoreNatural fiber composites: Growing to fit sustainability needs
Led by global and industry-wide sustainability goals, commercial interest in flax and hemp fiber-reinforced composites grows into higher-performance, higher-volume applications.
Read MoreCombining multifunctional thermoplastic composites, additive manufacturing for next-gen airframe structures
The DOMMINIO project combines AFP with 3D printed gyroid cores, embedded SHM sensors and smart materials for induction-driven disassembly of parts at end of life.
Read MoreRead Next
VIDEO: High-volume processing for fiberglass components
Cannon Ergos, a company specializing in high-ton presses and equipment for composites fabrication and plastics processing, displayed automotive and industrial components at CAMX 2024.
Read MoreAll-recycled, needle-punched nonwoven CFRP slashes carbon footprint of Formula 2 seat
Dallara and Tenowo collaborate to produce a race-ready Formula 2 seat using recycled carbon fiber, reducing CO2 emissions by 97.5% compared to virgin materials.
Read MoreDeveloping bonded composite repair for ships, offshore units
Bureau Veritas and industry partners issue guidelines and pave the way for certification via StrengthBond Offshore project.
Read More