Lanxess reveals highly sustainable Scopeblue composite material series
PA6 glass fiber-reinforced compound under Lanxess’ new Scopeblue series is made from 92% sustainable raw materials, with content goals headed toward 100%.
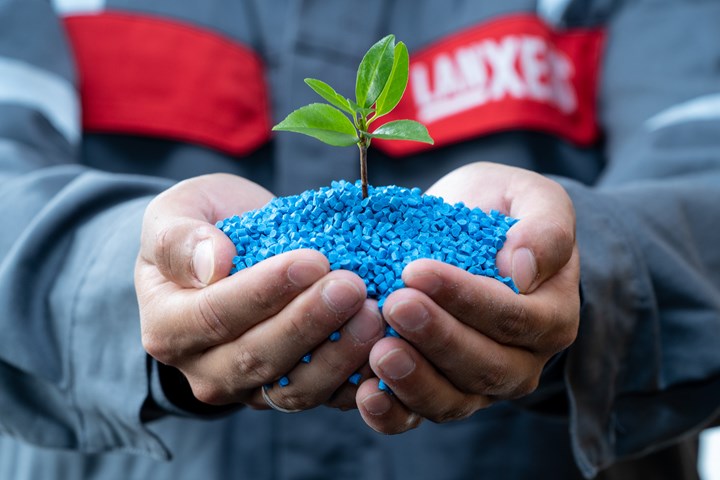
Lanxess is offering a new, particularly sustainable product under the name Durethan BLUEBKV60H2.0EF. Photo Credit: Lanxess
Lanxess (Cologne, Germany) introduces its latest product, Durethan BLUEBKV60H2.0EF, a glass fiber-reinforced compound that uses 92% sustainable raw materials, more than other prime quality glass-fiber-reinforced plastic the company notes. The new easy-flowing plastic grade is the first product in Lanxess’ new Scopeblue series, which identifies products that either consist of at least 50% circular (recycled or bio-based) raw materials, or whose carbon footprint is at least 50% lower than that of conventional products.
“A carbon-neutral future can become reality only if we start using more sustainable products,” says Frederique van Baarle, who heads the High-Performance Materials (HPM) division at Lanxess. “Our first product marketed under the Scopeblue brand represents a real solution for the circular economy. The compound is a certified premium material that’s based on sustainable raw materials.”
For example, cyclohexane is one raw material used in the production of the polyamide-6-based (PA6) product, and comes from a sustainable source, meaning it is either bio-based, recycled bio-based or produced by means of chemical recycling. Durethan BLUEBKV60H2.0EF is also strengthened with 60% by weight of glass fibers comprising industrial glass waste instead of mineral raw materials. Moreover, the alternative raw materials that Lanxess uses in the precursors for PA6 are chemically identical to their equivalents of fossil origin (“drop-in solutions”), so Durethan BLUEBKV60H2.0EF is reported to exhibit the same characteristics as the virgin material and can be processed just as easily using the same production tools and facilities with no conversion work needed.
“This high-strength, high-rigidity structural material can be deployed wherever its purely fossil-based equivalent, Durethan BKV60H2.0EF, has traditionally been used in series production — so in automotive construction for the production of car front ends, brake pedals and oil pans,” says Dr. Guenter Margraf, head of global product management at HPM.
Nevertheless, developers are setting their sights on more than 92% sustainable raw materials. “We’re currently working on increasing the content of sustainable raw materials in this compound to 100%,” says Margraf. This requires ammonia synthesized with carbon-neutral hydrogen. Over the medium term, the specialty chemicals company is also planning to replace the additives used in its plastics with sustainable equivalents.
With Durethan ECOBKV30H2.0, ECOBKV35H2.0 and ECOBKV60XF, Lanxess also recently unveiled three PA6 compounds containing 30%, 35% and 60% by weight respectively of recycled fiber made from glass waste as calculated using the ISCC Plus-certified mass balance method (defined below). In response to major customer demand, this product family has been extended over the past few months to include even more compounds based on PA6 and PA66. Lanxess is also using the recycled glass fibers for the mechanical reinforcement of its Pocan-brand polybutylene terephthalate (PBT) compounds. Early products include Pocan ECOB3235 and the flame-retardant ECOB4239, each of which contain 30% by weight of recycled glass fibers as calculated using the certified mass balance method.
Lanxess notes that the sustainable origin of all of its raw materials is certified to ISCC Plus (International Sustainability and Carbon Certification). This applies to Lanxess production sites in Antwerp, Belgium and Krefeld-Uerdingen, Germany, as well as all precursors originating exclusively from suppliers that are also ISCC Plus-certified.
Related Content
Microwave heating for more sustainable carbon fiber
Skeptics say it won’t work — Osaka-based Microwave Chemical Co. says it already has — and continues to advance its simulation-based technology to slash energy use and emissions in manufacturing.
Read MoreBio-based acrylonitrile for carbon fiber manufacture
The quest for a sustainable source of acrylonitrile for carbon fiber manufacture has made the leap from the lab to the market.
Read MoreRecycling end-of-life composite parts: New methods, markets
From infrastructure solutions to consumer products, Polish recycler Anmet and Netherlands-based researchers are developing new methods for repurposing wind turbine blades and other composite parts.
Read MoreNovel composite technology replaces welded joints in tubular structures
The Tree Composites TC-joint replaces traditional welding in jacket foundations for offshore wind turbine generator applications, advancing the world’s quest for fast, sustainable energy deployment.
Read MoreRead Next
Lanxess launches renewable, biocomposite material
The material combines natural flax fibers with bio-based polylactic acid, which acts as the matrix, for a material that is 100% recyclable.
Read MoreAll-recycled, needle-punched nonwoven CFRP slashes carbon footprint of Formula 2 seat
Dallara and Tenowo collaborate to produce a race-ready Formula 2 seat using recycled carbon fiber, reducing CO2 emissions by 97.5% compared to virgin materials.
Read MoreDeveloping bonded composite repair for ships, offshore units
Bureau Veritas and industry partners issue guidelines and pave the way for certification via StrengthBond Offshore project.
Read More