CompoTech launches standard range for carbon finer epoxy beams
Produced via AFP and precision press molded results in a high-strength carbon epoxy composite beam with 10-15% higher stiffness in the axial direction.
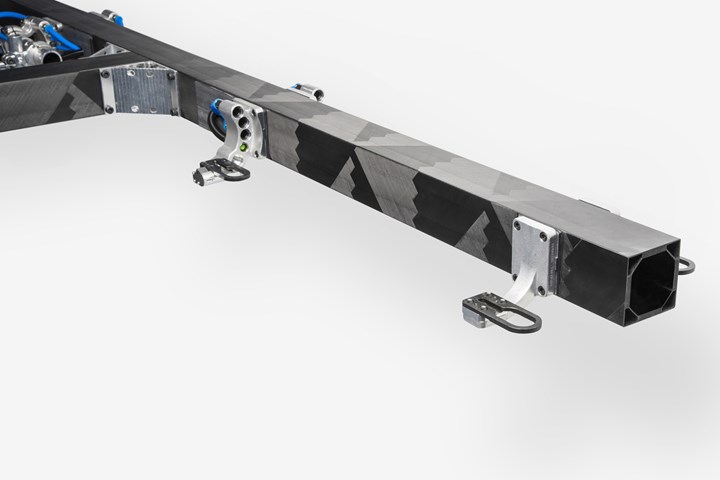
Standard connected beam used for T-boom applications in press shop manipulation. T-joint and attachments are made by bolting to the inserts placed in the corners of the profile. Source | CompoTech
CompoTech (Sušice, Czech Republic) has recently launched a new standard range of lightweight carbon finer (CF) epoxy composite beams in round tubes and square-shaped options and sizes, which can be specified instead of steel.
CompoTech says the standard square beams are produced from graphite and PAN carbon fibers using its automated robot-assisted filament placement technique, which places continuous fibers axially along the beam length. The result is a high-strength carbon epoxy composite beam with 10-15% higher stiffness in the axial direction and up to 50% greater bending strength compared to a conventional filament wound beam with the same dimensions.
All CompoTech beams are produced with automated filament placement (AFP) and precision press molded using a wet, two-part epoxy resin system. Curing is a two-stage process, first at room temperature to remove any residual stresses during molding that can cause deformation over time, then post mold curing in an oven. Compared with pultrusion, CompoTech says, its pressing technique provides a precision CF epoxy beam with very high dimensional accuracy and a close tolerance surface finish, which typically does not require costly CNC finish machining.
According to CompoTech, its carbon composite beams have enabled modular industrial tooling system producers, such as Bilsing Automation GmbH (Attendorn, Germany), to replace much heavier steel and aluminum beams, providing significant production benefits such as faster operating speeds and higher productivity; less vibration and more rapid damping; heavier load handling capabilities on the same line; lower energy consumption and lifetime operating costs; and easy assembly for structures needing bolted connections.

CompoTech winding of a graphite and PAN carbon fiber epoxy square beam. Source | CompTech
Successful applications in the aerospace, agricultural, automotive, metrology, marine and sports equipment market sectors for CompoTech products include industrial machine tool beams; drive shafts; automated automotive press line T-booms, structural frames and crossbars; crop sprayer booms; aerospace structures; yacht masts and spars; and composite bike frames.
The choice of standard square beam options includes hollow cornered ‘bolt together’ connector beams to extend length, and beams designed with reinforced corners for added stiffness, damping and load bearing performance.
Standard square beams are available in sizes from 60 x 60 x 5mm wall thickness, weighing 1.7 kg/m, with an E (elasticity) Modulus in the axial direction of 196 GPa, up to the largest beam 200 x 200 x 8mm, weighing 4.19kg/m, with E Modulus of 210 GPa, matching tool steel. The stiffest design achieves an E Modulus of 327 GPa, which is said to be 69% stiffer than stainless steel (193 GPa) and 56% stiffer than tool steel (210 GPa). Square beam lengths vary from between 2.3-5.0m depending on the size.
Standard CF epoxy round tubes, which have an E Modulus of 90 GPa, are manufactured using PAN carbon fibers. Tubes are available in sizes from a 428mm inside diameter x 4mm wall thickness, weighing 6.92 kg/m down to 10mm inside diameter x 2mm wall thickness, weighing only 0.11 kg/m. Standard tubes lengths are between 3.6-7.8m, depending on the diameter.
Both standard tubes and square beams are available in quantities from one-off to multiple batch orders. On request, CompoTech says it will look to add additional sizes to the standard round and square beam ranges, as well as continuing to offer its bespoke design and manufacturing service for industrial beams and other CF composite components to meet specific customer requirements.
Related Content
PEEK vs. PEKK vs. PAEK and continuous compression molding
Suppliers of thermoplastics and carbon fiber chime in regarding PEEK vs. PEKK, and now PAEK, as well as in-situ consolidation — the supply chain for thermoplastic tape composites continues to evolve.
Read MorePlant tour: Joby Aviation, Marina, Calif., U.S.
As the advanced air mobility market begins to take shape, market leader Joby Aviation works to industrialize composites manufacturing for its first-generation, composites-intensive, all-electric air taxi.
Read MorePlant tour: Albany Engineered Composites, Rochester, N.H., U.S.
Efficient, high-quality, well-controlled composites manufacturing at volume is the mantra for this 3D weaving specialist.
Read MoreCryo-compressed hydrogen, the best solution for storage and refueling stations?
Cryomotive’s CRYOGAS solution claims the highest storage density, lowest refueling cost and widest operating range without H2 losses while using one-fifth the carbon fiber required in compressed gas tanks.
Read MoreRead Next
Developing bonded composite repair for ships, offshore units
Bureau Veritas and industry partners issue guidelines and pave the way for certification via StrengthBond Offshore project.
Read More“Structured air” TPS safeguards composite structures
Powered by an 85% air/15% pure polyimide aerogel, Blueshift’s novel material system protects structures during transient thermal events from -200°C to beyond 2400°C for rockets, battery boxes and more.
Read MoreVIDEO: High-volume processing for fiberglass components
Cannon Ergos, a company specializing in high-ton presses and equipment for composites fabrication and plastics processing, displayed automotive and industrial components at CAMX 2024.
Read More